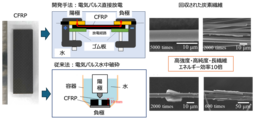
2024年12月16日
早稲田大学
新技術でCFRPから炭素繊維を加熱・薬剤レス、エネルギー効率10倍で回収
資源循環型社会の構築に向け、処理困難な材料の前処理法として期待
詳細は、早稲田大学HPをご覧ください。
発表のポイント
●電気パルス直接放電法を用いて炭素繊維強化プラスチック(CFRP)から炭素繊維を効率的に回収する手法を開発
● 開発技術は、加熱や薬剤を必要とせず、従来の破砕法に比べ長繊維で、加熱法に比べ高強度の炭素繊維を回収可能。また、従来の電気パルス法をさらに改良し、エネルギー効率10倍増を達成
● 現状では有効な解体方法がないCFRP廃棄物の前処理法として有望
炭素繊維強化プラスチック(CFRP)※1は、高強度かつ軽量な特性から航空機や自動車、風力発電など広く利用されていますが、そのリサイクルは困難であり、資源循環型社会の構築において大きな課題となっています。
早稲田大学理工学術院の所千晴(ところ ちはる)教授、同大学大学院院創造理工学研究科博士課程1年の佐藤啓太(さとう けいた)、同大学カーボンニュートラル社会研究教育センターの犬束学(いぬつか まなぶ)准教授、同大学理工学術院の小板丈敏(こいた たけとし)講師らの研究グループは、電気パルス直接放電法を用いて、CFRPから炭素繊維を効率的かつ高純度に回収する新技術を開発しました。
従来の電気パルス水中破砕法と比較し、新規法ではジュール熱発熱と絶縁破壊による樹脂の気化と膨張力を活用して、炭素繊維の長さや強度をほぼ維持したまま回収可能であることを示しました。さらに、新規法ではエネルギー効率が従来法の約10倍高いことも確認されました。本研究は、従来の破砕法や加熱法だけでは困難であったCFRP廃棄物の高効率で低環境負荷なリサイクルに新たな可能性を提供するものです。
【画像:https://kyodonewsprwire.jp/img/202412131632-O2-YtINsAtx】
図:本研究にて開発した電気パルス直接放電法
本研究成果は、国際学術出版社であるNature Research社発行による『Scientific Reports』誌に2024年11月30日(土)(現地時間)に掲載されました。論文名:Efficient recovery of carbon fibers from carbon fiber-reinforced polymers using direct discharge electrical pulses
キーワード:
サーキュラーエコノミー、資源循環、マテリアルリサイクル、CFRPリサイクル、革新的リサイクル技術、炭素繊維、廃棄物削減、風力発電、水素タンク
(1)これまでの研究で分かっていたこと
CFRPは、軽量で高い強度を持つため、航空機、自動車、風力発電、スポーツ用品など、多岐にわたる分野で使用されています。一方で、CFRPのリサイクルは困難であり、特に樹脂マトリックスから炭素繊維を分離するプロセスが課題となっています。
従来のリサイクル方法として、粉砕、熱分解、化学分解が検討されてきました。しかし、粉砕では炭素繊維が短くなり、その強度が著しく低下します。熱分解では、樹脂を高温で燃焼させることで分離が可能ですが、CO2排出への懸念や、炭素繊維の強度が50~85%低下するという問題があります。化学分解では、有機溶媒を使用して樹脂を溶解しますが、高価な設備と環境への影響が課題となっています。
近年、電気パルスを用いた手法として、水中破砕法が提案されました。この方法では、水中の電気パルス放電より生じる衝撃波を利用して材料を破砕しますが、数百回の放電が必要であり、炭素繊維と樹脂の選択的な分離には限界があります。
このように、CFRPにはより効率的で環境負荷の低いリサイクル技術の開発が求められてきました。
(2)今回の研究で新たに実現しようとしたこと、そのために新しく開発した手法
CFRPのリサイクルにおいて効率化と環境負荷の低減を実現するため、従来課題とされていた炭素繊維と樹脂の分離プロセスに革新をもたらす「電気パルス直接放電法」を新たに開発しました。この方法では、高電圧パルスをCFRP内部に直接放電することで、ジュール熱と樹脂の気化による膨張力を利用し、効率的に繊維と樹脂を分離します。
従来の電気パルス水中破砕法は、水中への放電によって生じる衝撃波を利用して分離を行っていましたが、直接放電法は電気パルスのエネルギーをより直接的にCFRP内部に伝えることが可能です。この結果、回収された炭素繊維は元の強度の81%を保持し、従来法に比べエネルギー効率が約10倍高いことが確認されました。また、直接放電法で得られた繊維には付着樹脂が少なく、表面のクラックや劣化もほとんど見られず、再利用の可能性が飛躍的に向上しました。
(3)研究の波及効果や社会的影響
本研究では、CFRPリサイクルの課題であった高エネルギー消費と炭素繊維の品質低下を同時に解決できることを示しました。ジュール熱の利用により、短時間で樹脂を気化させ、繊維を効率的に分離するこの技術は、環境負荷を最小限に抑えながら、航空機や風力発電などで発生するCFRP廃棄物の持続可能な資源循環型社会構築に貢献すると期待されます。さらに、この技術は、リチウムイオン電池など他の複合材料や産業廃棄物への応用可能性も秘めており、幅広い分野での資源活用を促進し、持続可能な社会の実現に大きく貢献することが期待されます。
(4)課題、今後の展望
本研究で開発した電気パルス直接放電法は、CFRPのリサイクルにおいて多くの可能性を示しましたが、いくつかの課題が残されています。まず、1回のパルス照射で回収される炭素繊維の量が少ないことが挙げられます。このため、繰り返し照射を含むプロセスの最適化や、よりCFRP内部に効率的に放電を誘導できる電極構造の改良が求められます。
さらに、回収された炭素繊維の方向性が揃っていない点は、再利用プロセスにおける課題となっています。これを解決するためには、回収繊維を均一に処理できるプロセスの開発や、新たな用途への適用可能性を検討する必要があります。
また、現在の実験室規模から、産業的スケールへの拡大に際して効率やコストの検証が必要です。本技術を工業的にスケールアップする際には、現在使用している装置が特殊であることから、装置製造コストの低減や大規模処理への対応が重要です。この点について、装置の汎用性を高める設計や運用コストを削減する方法の検討が必要です。
(5)研究者のコメント
サーキュラーエコノミーを実現するためには、本研究で取り組んだような解体技術の高度化が必要不可欠です。これまでは破砕粉砕や人手による作業に依存していましたが、環境負荷を低減し、労働集約的でないプロセスを実現するには、従来の方法に代わる革新的な技術が求められます。本研究で提案した電気パルス直接放電法のような新たな外部刺激を利用した技術は、処理が困難な材料の前処理法として大きな可能性を秘めています。今後もこれらの技術を発展させ、資源循環型社会の構築に貢献していきたいと考えています。
(6)用語解説
※1 炭素繊維強化プラスチック(CFRP)
炭素繊維強化プラスチック(Carbon Fiber Reinforced Plastic:CFRP)は、強化材として炭素繊維と母材(マトリックス樹脂)としてプラスチックを複合してできる素材。炭素繊維が持つ「導電性・耐熱性・低熱膨張率・反応特性・自己潤滑性・高熱伝導性」といった特徴を兼ね備え、様々な用途へ幅広く使われる。
(7)論文情報
雑誌名:Scientific Reports
論文名:Efficient recovery of carbon fibers from carbon fiber-reinforced polymers using direct discharge electrical pulses
執筆者名(所属機関名):所千晴* (早稲田大学理工学術院)、佐藤啓太(早稲田大学大学院創造理工学研究科)、犬束学(早稲田大学カーボンニュートラル社会研究教育センター)、小板丈敏(早稲田大学理工学術院) *責任著者
掲載日時(現地時間):2024年11月30日(土)
DOI:https://doi.org/10.1038/s41598-024-76955-0
(8)研究助成
科研費 基盤研究B 電気パルスを外部刺激とした高選択性分離技術確立のための機構解明 所千晴(早稲田大学)23K25037